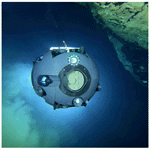
Underwater measurements with UX robots; a new and available tool developed by UNEXUP
Norbert Zajzon
Boglárka Anna Topa
Richárd Zoltán Papp
Jussi Aaltonen
José Miguel Almeida
Carlos Almeida
Alfredo Martins
Balázs Bodó
Stephen Henley
Márcio Tameirão Pinto
Gorazd Žibret
The UNEXMIN (Horizon 2020) and UNEXUP (EIT RawMaterials) projects developed a novel technology to send robots and even autonomously deliver optical images, 3D maps and other georeferenced scientific data from flooded underground environments, like abandoned mines, caves or wells. The concept turned into a market ready solution in seven years, where the last few years of field trials of the development beautifully demonstrating the technology's premier capabilities. Here in this paper, we focus on the wide variety of environments, circumstances and measurements where the UNEXMIN technology can be the best solution or the only solution to deliver certain research or engineering data. These are obtained from both simple and complex environments like different mines and caves, small and large cavities, long and tight tunnels and shafts, different visibility conditions, even different densities of the liquid medium where UX robots operated.
- Article
(9052 KB) - Full-text XML
- BibTeX
- EndNote
Raw materials are the foundation stones of many sectors of the modern societies (Bobba et al., 2020). Europe is extremely dependent on reliable raw material supplies – as raw materials are the foundation stones of many sectors of the society – and nowadays ca. 96 % of the used raw materials arrive from outside EU. If a commodity is mined by only one or few countries in the world, trade restrictions for political reasons can adversely impact supply chains. A good example is when China limited rare-earth elements (REE) export in 2008 exacerbating a global financial/economic crisis. These acts pushed the EU to create the first version of the EU Raw Material Initiative (RMI) in 2008 (European Commission, 2008). This document orders the regular assessment of the criticality of the raw materials, which is summarized in the Critical Raw Materials (CRM) list (earlier Critical Element list). The first CRM list contained 14 elements (like beryllium, cobalt, indium), and element-groups (e.g. REE, or platinum group elements (PGE)), but this list is continuously growing. The recent CRM list (from 2020) contains 30 commodities (Blengini et al., 2020). To solve the supply issue – in the absence of a well-maintained global trade – the possibilities are primary production, recycling and substitution of these raw materials. Even with increasing recycling and with substitution, primary mining will be necessary even in long term assuming a growing, developing society and the green transition. The primary mining usually begins with exploration activities which can be divided between “green-field” and “brown-field” exploration. The “green-field” exploration means finding ore deposits in the areas of no historic mining activities, while “brown-field” exploration is conducted on the areas of known historic mining activities. As Europe has been extensively mined for centuries, more than 30 000 abandoned mines were identified all over the continent, giving huge potential in “brown-field” exploration and the potential of reopening mines to produce the needed commodities.
The European Commission (2008) also developed the raw materials strategy of the EU, which is based on three pillars: (1) Fair and sustainable trade of raw materials in the global market, (2) Sustainable raw materials production inside EU, and (3) Effective resource management and use of secondary raw materials with recycling. The second pillar defines the necessity to improve the legal framework of exploration and exploitation of raw materials. Also, the necessity to improve knowledge of raw materials availability inside EU with the development of innovative exploration and exploitation methods, which can achieve the “biggest economic profit and environmental advantage”. Based on the RMI, an action plan was developed, which is the Strategic Implementation Plan (SIP) for the European Innovation Partnership on Raw Materials (European Commission, 2013). This SIP (in points 1.2 and 1.3) describes the way of development of exploration and extraction methods by (1) new exploration techniques, (2) automated mining techniques and (3) utilization of small deposits with economic and environmentally sound technologies. To facilitate the above described, the Horizon 2020 and Horizon Europe framework programmes allocated resources for these purposes to incubate appropriate innovations towards development of market ready technologies.
Parallel to the above actions the European Commission founded the European Institute of Innovation and Technology (EIT) in 2008, where they brought together the so called “knowledge-triangle” where universities, research institutes and industry harmonize their collective actions. Within the EIT in 2015, EIT RawMaterials has been established, which is the biggest association, community in the raw materials sector. This enables support, by numerous calls and grants, of closer to market-ready innovations.
Our idea to help raw materials exploration was to develop autonomous submersible robots, which are capable of entering flooded, abandoned mines to create 3D maps and to deliver visual and geoscientific information which help to assess the potential of the reopening the mine in a safe, economic and environmentally friendly way without the need of dewatering. The technology was developed by an international team of scientists during the UNEXMIN (https://www.unexmin.eu/, last access: 1 September 2023) Horizon 2020 project (2016–2019) and the UNEXUP (https://unexup.eu/, last access: 1 September 2023) EIT RawMaterials project (2020–2022). The concept was proven in various environments. Besides technological upgrades, the UNEXUP project focussed also on marketing and commercialization through UNEXMIN Georobotics Ltd. (https://unexmin-georobotics.com/, last access: 1 September 2023), a spin-off company of the consortium. Below we describe the achievements and the current capabilities of the technology.
The first generation of robots was built within the UNEXMIN project, which aims to construct an autonomous explorer of flooded mines. The work started at the beginning of 2016 with a quite extensive designing period to be able to turn the conceptual model into a working prototype. Robot's size, shape and required capabilities were defined at this stage to assure that the robot will be able to explore the targeted mines. The team decided that the UX robots will have spherical shape, 60 cm diameter and the 500 m diving depth capability. As the submersible buoyancy need to be neutral, or close to neutrally buoyant in water to be able to move with minimal energy, an approx. 110 kg weight target was derived from the shape and diameter. The functionalities and capabilities of the robot were developed together with the future potential customers, where the stakeholder requirements had a strong influence on the final selection of instruments. After the first design concepts were collected from the teams responsible for the different modules, we ended up with a model approx. 3 times the weight and 4 times the volume available. Thus, miniaturisation was the toughest part of the work, which extended the design period. From the beginning two different structural concepts were considered: the “open-frame” design and the “closed-hull” design. The “open-frame” design is popular in robotics allowing easy adjustability and flexibility, by placing the different modules in separate, smaller pressure casings which are attached to a weight-carrying frame. Contrary to this, the ”closed-hull” design is similar to submarines, where one large pressure-tolerant hull protects everything in the vehicle. The “closed-hull” concept gives the maximum available useful space and weight, while the “open-frame” concept can have better mobility, easier repair of broken parts, better adjustability, and more reliability if a leak happens. For the first robots, the “closed-hull” concept was selected to maximize the available space to help the miniaturisation. By this work the first UX-1a robot – called Nata – was built in early 2018 (Martins et al., 2018). This robot, with its slightly modified sisters UX-1b and UX-1c was extensively tested for two years. By the end of the UNEXMIN project, the technology reached the TRL 6 level (technology readiness level).
Based on the success of the UNEXMIN project, the next phase of development was submitted to EIT RawMaterials as an upscaling project to mature the technology and push it closer to the market (Pinto et al., 2020). With our developed knowledge, and with the four years development on the global electronic components market, we decided to change to “open-frame” design, which concept was proven by Mara – a robot – even before the UNEXUP upscaling project started. During this three years long project, the second generation of UX robots was designed, built and tested. This generation has two robots: the UX-1Neo and the UX-2Deep. Their dimensions had to be enlarged a bit, with the length of the robots extended to 70 cm, still keeping the 60 cm diameter in width and height resulting in a slightly elongated ellipsoid. Contrary to the dimension their weight is lighter than the UX-1 series due to the spaces among the different modules (UX-1Neo is 93 kg, UX-2Deep is 100 kg). UX-1Neo (called Neo) has the same 500 m depth rating as the UX-1a series, but its mobility, flexibility and usability are immensely extended. The UX-2Deep, the final product of the project has a somewhat greater weight, as it has all the capabilities of Neo, but has to support the 1500 m depth rating. The evolution- and the different members of the UX robot family can be seen in Fig. 1.
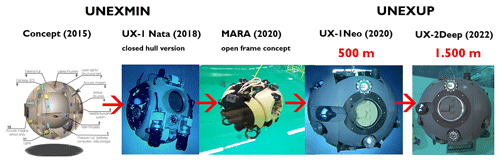
Figure 1The evolution- and the different members of the UX robot family until now (2023) (second from right image © UNEXUP).
The second generation UX robots has a battery for 8–10 h (depending on the use), 500/1500 m depth rating, high-end IMU (Inertial Motion Unit), a four-beam DVL (Doppler Velocity Log), three acoustic sonars (including a 256 beam scanning sonar), six camera modules covering all directions in the same time with special lighting units. These cameras with the special lighting are called SLS (Structured Light System), and can use regular white-light illumination, or UV-light for UV-fluorescent imaging, or the real novelty which is a projected rotating green-laser light stripe which allows a millimetre-accurate 3D space measurement if the visibility of the water allows its use. In addition to the navigation and 3D mapping tools, a set of “geoscientific” tools are also available including a water parameter measuring unit (including electrical conductivity, pH, oxygen fugacity, temperature), water sampler, three-axis flux-gate magnetometer, total gamma-ray counter, and a hyperspectral camera (460–860 nm).
All the members of the UX robot family were extensively tested and used on the field in different environments, but logically, the second generation (UX-1Neo and UX-2Deep) of the robots were tested in the most complex environments, as well as they were used in completely commercial missions. UX-1Neo was built by the end of 2020, and the first missions started in early 2021. In this chapter the most interesting field missions are presented to illustrate different environments and unique measurement possibilities available by this technology.
3.1 Urgeiriça (Portugal) uranium mine
Urgeiriça is an abandoned uranium mine, which is almost completely flooded (water level is ca. 7 m below the surface), easy to access and it is at a short distance from the laboratory of INESCTEC making it an ideal site to test and validate our robots since the first visit in 2018. It was obvious to have this test site as a first one outside of the laboratory in February of 2021 for the UX-1Neo also.
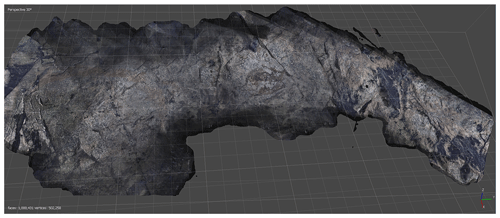
Figure 23D optical photogrammetry model from a part of the Urgeiriça uranium mine, Portugal. The black uranium ore is well visible in the granite.
For the first dive, the robot reached the available bottom of the mine which is blocked at (186 m) with rock debris. During the dives, we test all the systems of the robots, e.g., the Fig. 2 produced optical photogrammetry model, where the black uranium ore is visible in the granite.
If the water quality allows creation of georeferenced 3D optical photogrammetry models, than it is a powerful tool to visualize and understand the 3D geometry of the mines, and especially can help greatly to understand the geology. Depending on the available visualization tool the created model can be observed on a monitor, or in a VR headset.
3.2 Csór (Hungary) drinking water-well
At Csór, Hungary an important karstic drinking water-well is located which supplies the majority of the drinking water for Székesfehérvár – a small city with ca. 100 000 citizens. With the water table rising significantly in the area related to the abandoned bauxite mining activity which was extensive for decades, the well needed a strong reconstruction. To shorten the reconstruction time, a 3D map of the well accurate to a few centimetres had to be produced, which also allowed simulation of the movements of large pieces in the well. Moreover, a further constraint on this mapping was that it had to be done by a robotic survey and not by scuba-divers, as everything which goes into the well must go through a rigorous, properly defined cleaning process allowing continuous production, or water extraction must be stopped until cleaning of the entire well, which takes days in the case of human divers. It was no problem to soak the UX-1Neo and the necessary optical cable in the cleaning fluid for hours, and perform the measurements in one long dive while the well was suppling drinking water with no problem. The created 3D model was helpful to plan the reconstruction in detail, and turned out accurate, with the reconstruction happening smoothly in 2022.
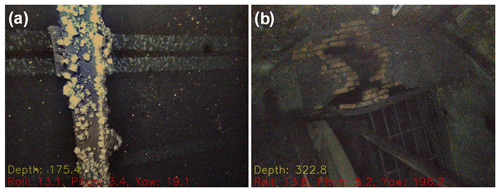
Figure 3(a) Few cm-size halite crystals grown from the brine, (b) blocked entrance of an adit only few metres from the Shaft 10 of Solotvyno salt mine.
3.3 Solotvyno (Ukraine), salt mine
Solotvyno is a historical salt mine called Aknaszlatina of the Austro-Hungarian Empire, which was operating for centuries till its accidental flooding in 2010. It is located in Ukraine less than 1 km from the River Tisza, which is the state boundary between Ukraine and Romania. Nowadays the mine is fully flooded and the area is collapsing rapidly growing extensive salt lakes above the former mine chambers. In the case of big flooding events the salt can reach the river, which is a potential natural hazard for the ecosystem. There are projects to monitor the situation and best plan the mitigation, which asked us to map the available parts of the mine. It was an extremely complex job and a very dangerous environment even for the UX robot. The technical difficulties include the fully saturated salt brine of the mine which is ca. 1.26 g cm−3 density, especially as the density changes with depth. It would be simpler to handle a constantly high density (that required ca. 24 kg extra lead weight to maintain neutral buoyancy), than the more than 100 m fresh water (1.00 g cm−3 density) followed by a few metres-thick transition zone and then the fully saturated brine (Fig. 3a). We trimmed the robot neutral in the high-density brine and designed a carrying cage (a special lift) to support it in lower density media. Of course, for all the sonars and DVL (Doppler Velocity Log) it was necessary to add a dynamic density calibration as the speed of sound is strongly dependent on the density for accurate navigation and measurement (Fig. 4). Some entrances of the mine were collapsed, or too dangerous to access. Two possible entry points were available, Shaft 9 and Shaft 10. In Shaft 9 there was a blockage which needed to be passed with extensive manoeuvring. UX-1Neo could do this when neutrally buoyant in the fresh water, but it was not possible to pass with the weight-adjusted robot and the carrying cage. The only possible point to dive was Shaft 10, which we measured with the robot down to −435 m, and with a separate water parameter measuring unit to the bottom at −506 m. The higher levels of the mine were blocked for example by a gate in −308 m (Fig. 3b). The lowest part of the mine was not accessible with the UX-1Neo, as the robot was calibrated to 50 bars, and here with the higher density also higher the pressure (e.g. at −435 m water-depth there was 47.5 bar pressure).
3.4 Camborne (UK), South Crofty mine
South Crofty is the last tin mine closed in 1998 in Cornwall related to greisenic and vein type Sn-Cu-Zn-Pb mineralization of the Variscan granite. As the tin prices significantly increased in the last years Cornish Metals Ltd. tries to reopen the mine, as it would be economic at current tin and copper prices. As the mine was ca. 800 m deep during its last operation, and now the water table is at ca. 60 m below the surface, significant, more than 700 m dewatering is planned, to remove ca. 8 million m3 of water from the workings, and requiring a double stage pumping system. The company plan to utilize the original pumping station at ca. 300 m current water depth in the New Cooks Kitchen shaft. They requested the 3D survey of the pumping station area if it is accessible, as there was a suspicion that access may be blocked by a gate from the shaft. It was a difficult dive, as the shaft was segmented, and the largest available space was ca. 1.2 m with poor visibility (ca. 10–15 cm) (Fig. 5a). The dive was successfully completed, but unfortunately the gate was locked to the pumping station at −287.7 m (Fig. 5b), preventing the detailed inspection. As the water is also planned to be utilised as a geothermal heat source the temperature profile of the thermal water in the shaft was also recorded during the dive.
3.5 Ashbourne (UK), Ecton mine
Ecton mine is a world-famous medieval Cu-(Zn-Pb) mine in the Peak District which was the World's deepest mine (−311 m) operating below the water level before these deeper workings were closed in 1854. Nowadays it is a National Monument site protected by law and operates as an educational mine for students and the public. From the beginning of the UNEXMIN project Ecton Mine Educational Trust (EMET) was in the consortium providing this ideal location to test our robots in an important archaeological site, from where the newest available information is at least 170 years old, the shafts and adits are narrow, and the exploited chambers are irregular and have a cheese-like structure. On this site we tested both generations of UX robots, visiting the site in 2019 with the UX-1a and UX-1b, and in 2022 with the UX-1Neo. In both missions, we discovered and measured previously unknown corridors, excavated halls, and connections as well as recording much geological and archaeological data.
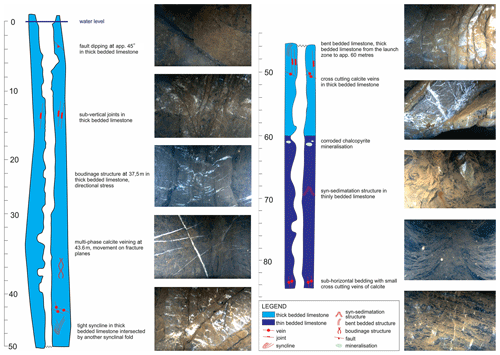
Figure 6The observed and interpreted geology of the 0–85 m section of the Winding shaft, Ecton mine, UK (image is adopted from Henley et al., 2019).
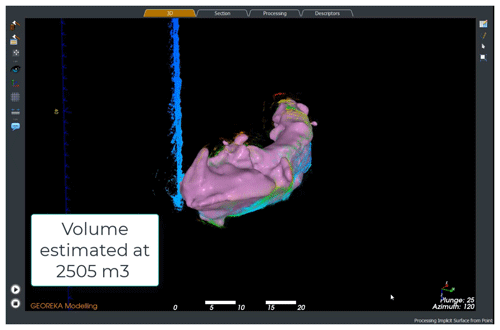
Figure 73D projection and volumetric measurement of the exploited ore lens at 56 m in the Winding shaft of the Ecton mine, UK.
The 3D photogrammetry allowed modelling of the geology of the mine (especially structural geology) from the walls (Fig. 6) and the accurate 3D model allowed different measurements, e.g., calculating the volume of an excavated ore lens (Fig. 7). Unfortunately, the two main available shafts of the mine are blocked at −117 and −125 m below the water level (probably backfilled, at least partially) thus the deeper levels of the mine cannot be accessed.
3.6 Budapest (Hungary), Kőbánya mine
Kőbánya mine, Budapest, Hungary was an interesting test site of the UNEXUP project as here the full autonomy and remote operation of the system were tested and demonstrated for the first time. Kőbánya in Hungarian means stone quarry, this area was an extensive underground housebuilding stone block mine with many tens of km in total length. After the mine closure, the workings were used for different storing-, cellar purposes, like three big beer brewing companies which operated hundred years ago, and parts of the system are still in use for such purposes. Some smaller separated parts of the mine become flooded as the extensive water extraction stopped with the declining beer brewing. Nowadays these areas with remaining mining equipment and beer brewing artefacts in the crystal-clear water make the place an interesting scuba diving target. This place supported excellent conditions to test the different instrumentation (Fig. 8), autonomous mapping and navigation of the UX-1Neo to map and navigate in this environment.
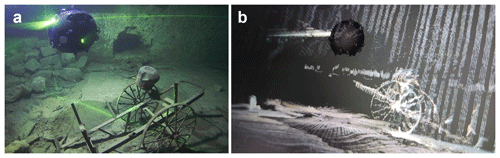
Figure 8(a) UX-1Neo is mapping the mine with SLS (the green lasers are well visible) (© UNEXUP), and (b) the real-time created 3D map of the area for navigation.
The selected location, so called “Park kút” contained small and bigger chambers, corridors and staircase a few hundred metres in length and ca. 30 m maximal water depth. For regular daily operation and sensor testing the robot control room was setup only few meters from the launching site. However, the robot in this case was also controlled and operated remotely from the other corner of Europe, when engineers from INESCTEC from their laboratory at Porto, Portugal, executed successful dives. The full autonomous tests of the robot were also scheduled here. The optical cable was removed, and the robot was sent to different missions without any communication, till the UX-1Neo returned back to the surface at the launching point. The big chamber with the different objects made that place too complex to start the autonomous missions there, but the rest of the place, the staircase, small room and corridor with ca. 300 m total length were mapped and delivered full autonomously by the UX system without any human intervention.
3.7 Hranice (Czech Republic), Hranice Abyss
Hranice Abyss is the deepest underwater cave on Earth. Before our mapping mission the cave was 404 m deep, reached by another ROV. The depth was impressive, but no good maps were available not only from the deepest part, but also from the upper areas, as that would require extreme scuba diver work without a specialized robot, like the UX. These maps are also the basis of the extensive geological exploration target to unlock the interesting formation and history of the cave, as it is located in an intensive CO2 degassing fault line.
In the Summer of 2022, the UNEXUP team joined forces with the Hranický Kras team of the Czech Speleological Society to map the upper 200 m section of the cave and create an accurate 3D model for scientific research. The mapping went so smoothly instead of the upper 200 m, the team mapped the known 404 m and went even deeper with the mapping down to −450.6 m setting the new bottom of exploration of the cave and setting the new World Record on 1 August. The corridor at the current end is enormous and goes even deeper, but at that time the UX-1Neo had a 500 m depth limit, thus the team decided to visit the place later with the more suitable UX-2Deep which is 1.5 km depth-rated. In addition to the excellent 3D map (Fig. 9), the UX robot also continuously measured the water parameters (EC, pH, oxygen fugacity, temperature) during the mapping supplying important data for the hydrogeologists.
3.8 Pforzheim (Germany), Käfersteige fluorite mine
Käfersteige mine is a candidate for re-opening and renewed fluorite production as fluorite has become a critical raw material for the EU. The mine is located in the Black Forest area of Germany. It is abandoned and was flooded ca. 30 years ago. Before the future dewatering of the mine the company wished to collect mining engineering and water quality data along the decline down to the bottom of the ore vein for better planning and also to visually confirm old data regarding the presence of the fluorite.
The depth of the dives was not significant, max. 140 m (though already problematic for scuba divers), but the lateral extent was more than 1300 m from the longest dive. This made this mission unique from robotic side, but also the collected UV-fluorescent images (Fig. 10) of the ore were a good opportunity for the geologists to test this tool.
The UNEXMIN technology made available the safe exploration of underground flooded spaces, both manmade and natural, like flooded mines and caves down to 1.5 km water depth. During such dives, the UX robots perform measurements and create 3D maps for multiple purposes. In seven years the two projects turned this concept into a real working solution where the service is available on the market for research and industry (https://unexmin-georobotics.com/, last access: 1 September 2023).
The above sites represent a wide variety of situations where the UX robots and technology can be used with their novel toolset and unique capabilities. The Urgeiriça uranium mine represents an example where the ore and the host rock can be distinguished visually, thus good visibility and optical features allow even georeferenced 3D photogrammetry nearby the other basic features. The Csór drinking well represents unique sites where special cleaning and safe operation avoiding pollution, is required as the water was directly pumped into the local drinking water network, till cm-accurate 3D mapping is needed for successful reconstruction work. The salt mine of Solotvyno is an example of an extreme environment where the salt-saturated brine is a huge challenge where the corrosivity of it is merely one of many problems including sensor calibrations. A big problem is the 1.25 g cm−3 density of the brine requiring an extra 25 % thus ca. 25 kg weight on the robot being neutral and able to float, while the weight must be carefully distributed not to change the centre of gravity of the robot. But the biggest challenge is how to overcome if this elevated density does not start from the surface, but there are different-density waterbodies for hundreds of meters with transition zones between them. The South Crofty Sn-W mine is a good example of sites with very limited visibility and all the navigation and mapping must rely mainly based on sonars. The Ecton mine is a special place being a UK National Monument, thus all the missions must be in harmony preserving this historical heritage, not even drilling a single hole into the walls. This is also a place where the 60 cm size of the robot is needed as being a medieval mine with narrow passages from minimal extraction of waste rock, and the 3D volumetric measurements can be well demonstrated in the big chambers of the mine. Kőbánya mine was the place where the capabilities of the UX robot were demonstrated with full autonomy without any cable thus any communication. Hranice Abyss is also unique not because of the World Record setting up the deepest dive in flooded caves, but because despite the not so good visibility, the enormous size of the chambers and complex structures of the walls the entire mapping was done in a single dive in 1 d's operation, demonstrating how powerful the technology is. The last site, the fluorite mine of Pforzheim is also a good example of the navigation and mapping capabilities, but instead of vertically, the horizontal dimensions are demonstrated, as the fluorite ore was investigated – even in UV using one of the robot's special “geo-tools” – more than 1.3 km from the launch site. To learn more about the sites and missions the related videos are available on the YouTube channel of the project: https://youtube.com/@unexup8632/videos (last access: 1 September 2023). The possibility to perform these measurements and collect these data underwater, without the need of dewatering, made this a cheaper and safer way than other alternatives, or in many cases the only possible way to do it. This technology opened a new segment of available data both for scientists and engineers.
No data sets were used in this article.
The authors contributed equally to this work. Conceptualization: NZ, RZP, JA, JMA, CA, AM, BB, SH, GZ. Investigation: NZ, BAT, RZP, JA, JMA, CA, AM, SH, MP, GZ. Methodology: NZ, BAT, RZP, JA, JMA, CA, AM, BB, SH, MTP, GZ. Visualization: NZ, BAT, RZP, JMA, CA, AM, SH, MTP. Writing – original draft preparation: NZ, BAT, SH, GZ. Writing – review & editing: NZ, BAT, RZP, JA, JMA, CA, AM, BB, SH, MTP, GZ.
The contact author has declared that none of the authors has any competing interests.
Publisher's note: Copernicus Publications remains neutral with regard to jurisdictional claims in published maps and institutional affiliations.
This article is part of the special issue “European Geosciences Union General Assembly 2023, EGU Division Energy, Resources & Environment (ERE)”. It is a result of the EGU General Assembly 2023, Vienna, Austria, 23–28 April 2023.
First of all, we would like to mention and thank for the hard work of the team, participating in the UNEXMIN and UNEXUP projects. This work allowed us to create the current UNEXMIN technology. Only a few of us are in the authors' list, but more than one hundred people contributed to the project with smaller or bigger efforts.
The UNEXMIN project was funded by the European Union through the Horizon 2020 research and innovation programme under the no. 690008 grant agreement. UNEXUP was funded partially by the European Union in EIT RawMaterials project no. 19160.
This research has been supported by the Horizon 2020 (grant no. 690008) and the EIT RawMaterials (grant no. 19160).
This paper was edited by Johannes Miocic and reviewed by Michael Berner and Nikolaus Sifferlinger.
Blengini, G.A., El Latunussa, C., Eynard, U., Torres de Matos, C., Wittmer, D., Georgitzikis, K., Pavel, C., Carrara, S., Mancini, L., Unguru, M., Blagoeva, D., Mathieux, F., and Pennington, D.: Study on the EU's list of critical raw materials (2020) – Final report, European Commission, Directorate-General for Internal Market, Industry, Entrepreneurship and SMEs, Publications Office, https://doi.org/10.2873/11619 (last access: 15 June 2023), 2020.
Bobba, S., Carrara, S., Huisman, J., Mathieux, F., and Pavel, C.: Critical raw materials for strategic technologies and sectors in the EU – A foresight study, European Commission, Directorate-General for Internal Market, Industry, Entrepreneurship and SMEs, Publications Office, https://doi.org/10.2873/58081 (last access: 1 June 2023), 2020.
European Commission: Communication from the Commission to the European Parliament and the Council – The raw materials initiative – meeting our critical needs for growth and jobs in Europe, COM(2008) 699 final, http://eur-lex.europa.eu/legal-content/EN/TXT/PDF/?uri=CELEX:52008DC0699&from=EN (last access: 15 June 2023), 2008.
European Commission: Strategic Implementation Plan for the European Innovation Partnership on Raw Material, https://single-market-economy.ec.europa.eu/sectors/raw-materials/eip/strategic-implementation-plan-sip_en (last access: 15 June 2023), 2013.
European Comission: Report on Critical Raw Materials for the EU, https://ec.europa.eu/docsroom/documents/10010/attachments/1/translations/en/renditions/pdf (last access: 15 June 2023), 2014.
Henley, S., Barnatt, J., Shaw, R., Žibret, G., Pučko, E., van Moerkerk, H., McLoughlin, M., Tweedie, J., Lopes, L., Sanchez, A., and Zajzon, N.: Geoscientific Evaluation of Pilots, UNEXMIN deliverable D7.6, https://www.unexmin.eu/download/unexmin-d7-6-geoscientific-evaluation-of-pilots/ (last access: 15 June 2023), p. 174, 2019.
Lukeš, J. and Souček, J.: https://hranickapropast.cz/mapy/ (last access: 15 June 2023), 2017.
Martins, A., Almeida, J., Almeida, C., Dias, A., Dias, N., Aaltonen, J., Heininen, A., Koskinen, K.T., Rossi, C., Dominguez, S., Vörös, Cs., Henley, S., McLoughlin, M., van Moerkerk, H., Tweedie, J., Bodo, B., Zajzon, N., and Silva, E.: UX 1 system design – A robotic system for underwater mining exploration, 2018 IEEE/RSJ International Conference on Intelligent Robots and Systems (IROS), 1–5 October 2018, Madrid, Spain, 1494–1500, https://doi.org/10.1109/IROS.2018.8593999, 2018.
Pinto, M. T., Žibret, G., Lopes, L., Bodo, B., and Zajzon, N.: UNEXUP: robot-based exploration technology for underground flooded mines, Adv. Geosci., 54, 109–117, https://doi.org/10.5194/adgeo-54-109-2020, 2020.