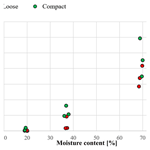
Laboratory assessment of corrosion rate of carbon steel ground heat exchangers
Alessandro Bortolin
Eloisa Di Sipio
Giovanni Ferrarini
Paolo Bison
Adriana Bernardi
Giorgia Dalla Santa
Antonio Galgaro
The materials used in the manufacture of geothermal heat exchangers for shallow geothermal applications play an important role in the overall system performance, especially if grout is not being used to seal the boreholes in which the heat exchanger is installed. The subject of this study is the durability evaluation of a vertical coaxial ground heat exchanger made of steel that is coupled directly to the ground. This solution minimizes the thermal resistance between the heat exchanger and the ground, but presents the important drawback of removing any protection toward the surrounding environment Among the materials proposed for manufacturing such vertical geothermal heat exchanger, carbon steel is suitable and have potential, due to its low cost and high thermal conductivity. The main disadvantage of this material is that it is strongly subject to corrosive attack, according to the chemo-physical properties of the underground. This study investigated the corrosion behaviour of carbon steel used in an experimental underground heat exchanger and assessed its durability over time. Corrosion rate of steel samples were measured in the laboratory by weight loss method after exposure over a specified period in a selected ground medium. Different ground conditions were tested, resulting in different densities and moisture contents of ground samples collected on the field. Based on the results, the corrosion rate of carbon steel is evaluated as a function of water content and rate of ground compaction. This information has allowed to advance more accurate quantitative forecast of the expected operational life of installed geothermal exchangers and their safety over time.
- Article
(1298 KB) - Full-text XML
- BibTeX
- EndNote
As practice of the European research projects Cheap GSHPs (European Commission, 2015), and GEO4CIVHIC (European Commission, 2018), a holistic approach has been taken to make shallow closed-loop geothermal energy more convenient, safe and efficient. During the implementation of the projects, various aspects were addressed, such as ground source heat pumps, secondary fluids, as well as drilling methods and the design of ground heat exchangers. Focusing on vertical ground heat exchangers (GHEs), the coaxial types have been investigated and improved by optimizing the general design (Pockele' et al., 2020). One of the new technologies being developed during GEO4CIVHIC is a methodology that allows both borehole drilling and pipe installation at the same time. This greatly reduces costs and opens up the possibility to have the pipe in direct contact with the ground. In this way, there is no extra thermal resistance between the heat transfer fluid and the ground because there is no injection of grout into the borehole. In fact, there is no annular gap at all, as result of the installation procedure. The only remaining thermal resistance due to a physical item is the pipe itself. Based on these advances, the research focused at further improving the system by exploring alternative GHE materials (Mendrinos et al., 2016; Boban et al., 2021) such as metals, that have very good thermal properties (Ashby, 2010; Ferrarini et al., 2020). Plastic represents the most common pipe material in shallow geothermal systems, despite its poor thermal properties, as it is affordable and does not degrade by corrosive attack. Corrosion of pipe used for GHEs is crucial because it leads to system failure and is thought to be an environmental hazard in the event of a liquid leak (in particular if antifreeze liquids are used). Stainless steel is resistant to corrosion but it is very expensive and thus not economically sustainable. Therefore, research moved to study the advantages and drawbacks of carbon steel, an affordable material that is characterized by an excellent thermal conductivity (Cadelano et al., 2021). Corrosion is renowned as a major problem for the long-term function and integrity of all kind of pipelines (Cadelano et al., 2016), including buried carbon steel components such as electric poles or pipelines. In the case of geothermal heat exchangers, this aspect is especially important as it causes damage beyond system failure. Indeed, the leakage of heat transfer fluid through corroded piping causes serious environmental problems. The mechanism of corrosion is variable and depends on the specific composition of the metal alloy and the local underground conditions. The dissolution of carbon steel is caused by electrochemical processes due to the presence of both oxygen and water. Additionally, other parameters, related to ground properties, can potentially enhance corrosion issues (Arriba-Rodriguez et al., 2018). Such parameters are pH, resistivity, humidity and oxygen. However, the operational criteria for assessing ground corrosion only take into account ground properties from a qualitative point of view. The corrosion rate, defined as the mass of metal per unit time destroyed, can be assessed using standard laboratory procedures based on measuring weight loss over time. These methods are used in many fields of engineering but not yet exploited in shallow geothermal systems. By applying these methods to metal samples such as GHE piping material buried under known conditions, it is possible to quantitatively assess the site-specific corrosion rate.
2.1 Definition of corrosion parameters
The severity of corrosion can be expressed by the corrosion rate (CR) that consists in the material loss over time of metals exposed to corrosive environments. Concerning geothermal components, it depends on the coupling of the metal constituting the outer pipe of the exchanger with a specific ground that can be found in the strata where the pipe is buried. Usually, CR is expressed in terms of depth of penetration, so in metric units it is millimeters per year. Corrosion rates can be measured in the laboratory according to standard test methods. They generally consist of exposing metal samples of known density and shape in a corrosive environment for a period of time. The material loss is then measured by gravimetric analyses. In this study, the ASTM G162-18 method (ASTM International, 2021) was applied to calculate the corrosion rate of structural carbon steel specimens. It is based on weight loss, which is expressed by the following Eq. (1):
where W is the weight loss (mg); A ist the area of the sample (cm2); ρ is the metal density (g cm−3); t is the time of exposure in corrosive environment (hours). CR (Corrosion Rate) is the weight loss of a pipe system or other metallic surfaces after exposure to a corrosive environment (mm yr−1).
This practice does not replicate all field conditions and variables existing underground, such as stray currents, microbiologically influenced corrosion, non-homogeneous electrochemical conditions, but it allows to simulate the most common and relevant conditions that determine the corrosiveness of a soil.
Corrosion rate is a useful parameter to assess the lifespan of metal-based buried structures, and therefore it also determines the maintenance requirements for components. Assuming, according to NACE Corrosion Engineer's Reference Book (Baboian et al., 1991), a uniform corrosion over the entire component surface, and CR as constant, obtaining the maximum theoretical lifetime of a buried pipe as Eq. (2):
It is worth remarking that the estimated lifetime refers to the complete destruction of the pipe. Actual service life should presumably be much shorter, especially if mechanical integrity is compromised due to external stresses or forces, e.g. water pressure, vibrations, etc. Moreover, the possible simultaneous corrosion attack on the internal side of the pipe is neglected in this study. The expected lifetime of any geothermal system is always limited. For the sake of having a reference value, in most cases the lifetime can be considered economically sustainable when it is over 30 years (Hähnlein et al., 2013) of actual service life.
2.2 Experimental process and samples preparation
The experiment was conducted by collecting the ground samples from a shallow geothermal site in the frame of GEO4CIVHIC project located in Padua, Italy. In such site, carbon steel groutless vertical experimental ground heat exchangers were installed. The samples were collected 1.5–1.8 m below ground level which is very shallow but consistent with the specific type of GHEs which are very short (average thermal exchange length is less than 7 m). In addition, it represents a worst-case scenario, as it was assumed that corrosion would be more critical near ground level due to the abundance of oxygen and water from precipitation. The ground samples typology is silty clay and the average measured pH is 8.16 at the sampling depth (New York State Department of Transportation, Geotechnical Engineering Bureau, 2015). A total of 30 specimens (i.e. 30 collected ground samples from the same location) were inserted in a container. Then, the parameters known to critically impact on the corrosion rate, as oxygenation (in relation to the compactness of the soil) and water content, were gradually changed. The samples were prepared according to the ASTM G162-18 (Standard Practice for Conducting and Evaluating Laboratory Corrosion Tests in Soils), also paying attention to the ground quantities and the specifications of the containers.
Firstly, the ground samples were dried in a ventilated oven at 105 ∘C constant temperature for several days, regularly monitoring their drop in mass to equilibrium. In order to evaluate the corrosion behavior of the soil with varying moisture content (MC), samples were prepared by artificially setting different quantities of water, as a fraction percentage of the saturation moisture content (SMC) of the soil materials. SMC is defined as the maximum amount of water that can be contained in a ground type when all pore spaces are filled with water. The reference moisture contents of the analyzed ground samples were: 0 %, 20 %, 40 %, 70 % and 85 % obtained by gravimetric method. By pressing the samples, two levels of density were arbitrarily obtained: 7 and 13 g cm−3 to simulate loose and compacted ground respectively. For each combination of MC level and compactness, three different ground samples were prepared for redundancy, as reported in Table 1.
Table 1Organization of tests. The numbers of tested ground samples for each MC and ground compactness level are reported.
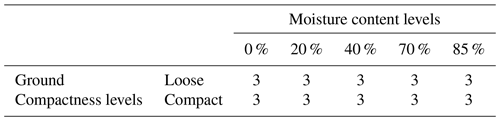
Subsequently, for each of the 30 polyethylene containers filled with ground with varying compactness and MC, a metal coupon of known size and mass was inserted inside, as schematized in Fig. 1.
The coupons were made of S235JRH carbon steel plates having surface area equal to 1.8 cm2. Oily greases or other corrosion inhibiting substances can be often found on metal components, as results of metal manufacturers practices to protect the metal from corrosion where no enamel or other proper passive anti-corrosion measures are present. Therefore, the coupons were cleaned by rinsing them in ethylic alcohol solution. The coupons were intended to simulate the outer pipe of the ground heat exchangers that were installed in the field, which are in fact made of carbon steel in direct contact with the ground, without grouting or filling in the borehole. The prepared containers, thus including the ground and the metal coupons, were sealed with plastic film, then kept undisturbed for an exposure time of 2304 h at constant room temperature. During that period, the moisture content was also kept constant by refilling the water if necessary. In fact, a periodic monitoring by gravimetric method were implemented to check the containers for possible weight loss due to water evaporation. Finally, the metal specimens were extracted, cleaned, rinsed with alcohol solution and then weighed to evaluate the mass drop. Finally, the corrosion rate for each of them was calculated according to Eq. (1).
The visual appearance of the carbon steel coupons surface after exposure to the corrosive ground environment is shown in Fig. 2 that depicts unaltered photographic images of some coupons at the end of the test. It is evident that the corrosive attack progressed the most in soil environments where the moisture content was higher.
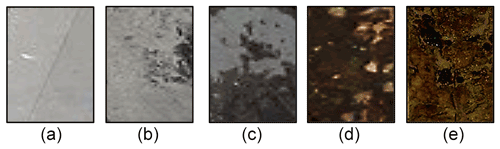
Figure 2Visual images of specimens after 2304 h exposition at different moisture contents; 0 % (a), 20 % (b), 40 % (c), 70 % (d) and 85 % (e). Ground density has no significant evidence on visual inspection.
The result of the gravimetric test shows that the corrosion rate increases non-linearly with the moisture content, as shown in Fig. 3.
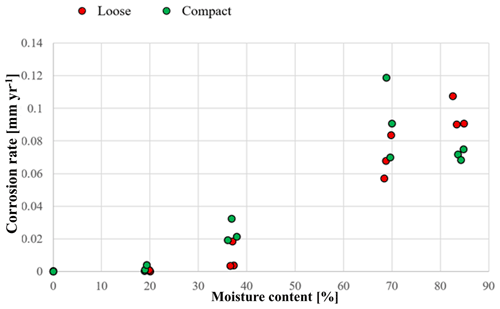
Figure 3Corrosion rate of metal coupons as function of moisture content. Red indicators refer to loose ground. Green indicators refer to compact ground.
Based on the results, the corrosion rate of the carbon steel coupons is highest (values of around 0.1 mm yr−1) at >70 % moisture content. At even higher moisture content, CR is greater for loose soil conditions. Corrosion rate is almost zero at 20 % water content. Nonetheless, CR it is not negligible for coupons exposed at 40 % of moisture content, especially in compact ground environment. At moisture content equal to 0 %, the corrosion attack is negligible. As expected, results indicate that the corrosion rate of carbon steel under constant boundary conditions is higher when the soil has a higher moisture content, so the water content percentage seems to affect more the metal corrosion compared to the rate of ground density. It can be hypothesized that at low moisture content, the lower rate of ground compaction limits the corrosion due to a drainage effect: the water, seeping through the interstices of the texture of the ground, flowed to the bottom of the container, away from the metal sample. At higher moisture content, higher rate of ground compaction enhances corrosion because it would favor a differential oxygenation. The evaluation of the corrosion rate allows to advance the forecast of the maximum expected life of the ground heat exchangers. The number of years necessary to corrode completely the carbon steel pipe was calculated according to Eq. (2), and taking into account a pipe wall thickness equal to 2 mm. Results are shown in Table 2. The measurement uncertainty has been expressed as the standard deviation σ over the three values obtained from the redundant specimens.
The corrosion rate values obtained as a function of the moisture content can also be used to define more refined durability models that take into account the effect of precipitations, which can be relevant for very shallow installations. The annual variation in soil moisture directly affects the CR, which would therefore not be constant. In order to evaluate the effect of considering CR not constant, the rainfall data of the studied site were recovered from the meteorological data collected by the ARPAV (Regional Agency for the Protection of the Environment of Veneto, https://www.arpa.veneto.it/bollettini/storico/2022/0234_2022_TEMP.htm, last access: 20 June 2022). Data record of Padua weather station was processed to obtain a simplified model of variable moisture content. Assuming the average number of rainy days and individual rain events over the last 10 years, the adjusted annual CR would be ca. 0.04 mm yr−1, which allows us to predict complete perforation of the pipe after about 50 years. However, the alternating cycles of wet-dry conditions as further aggravating parameters affecting the corrosion has not been considered, and it should be examined by future investigations.
In order to evaluate the durability of a new type of metal ground heat exchanger for shallow geothermal applications, a dedicated laboratory testing methodology was applied to assess the corrosiveness of the ground at the site where such GHEs were installed. Specifically, the test were mean to evaluate corrosion at very shallow depths, where corrosive attack is considered to be more critical due to the presence of moisture due to precipitations. Carbon steel metal samples were exposed in ground environment collected on site. The corrosion rate was evaluated, also as a function of the main parameters that are known to affect corrosion, i.e. water content and rate of ground compaction, the latter related to ground oxygenation. This way of evaluating the expected life is partial and takes into account only the main corrosion mechanisms in the underground environment, and does not consider other corrosion phenomena induced e.g., by bacteria, stray currents or presence of organic matter. However, the applied methodology represents a promising introduction in the field, because it provides an indication that would help assess sites when designing a geothermal system. Under constant conditions, the worst-case corrosion rate is within 0.1 mm yr−1 at the site under consideration, assuming a constant moisture content >70 %. In this context, the durability of a metal pipe with a wall thickness of 2 mm is approximately 20 years. This operational life expectancy would be below the acceptance threshold, therefore making it necessary to use an anti-corrosion protection.
The results of this study allow for the introduction of ground corrosiveness assessment as a suggested methodology for evaluating a site. In fact, it would provide site-specific and quantitative forecast of the expected life of the GHEs. Furthermore, this methodology can be easily adapted to replicate site specificities that can impact soil corrosivity, such as precipitations, temperature variations, etc.
If the ground samples are collected at different depths, it would also be possible to test different tube materials against the different lithologies present in the different layers. This would imply the interesting possibility of designing a new type of vertical ground heat exchanger built not in a single tube material, but in sections of different materials, that are selected to ensure optimal coupling with the corresponding ground layer. For example, plastic should be used in the most superficial layers, where corrosion is more significant due to a greater presence of water and oxygen, and metal in the deeper layers.
Code is available from the corresponding author on reasonable request.
Data is available from the corresponding author on reasonable request.
GC designed the study; GC, AB, EDS, GDS and AG developed the methods; GC, PB, AB and GF collected the data; GC and AB developed the numerical model. All the authors discussed the data and agree on their interpretation; GC wrote the manuscript. All the co-authors contributed to the final polishing of the manuscript.
The contact author has declared that none of the authors has any competing interests.
Publisher’s note: Copernicus Publications remains neutral with regard to jurisdictional claims in published maps and institutional affiliations.
This article is part of the special issue “European Geosciences Union General Assembly 2022, EGU Division Energy, Resources & Environment (ERE)”. It is a result of the EGU General Assembly 2022, Vienna, Austria, 23–27 May 2022.
This research has been supported by the European Union's Horizon 2020 (GEO4CIVHIC (grant no. 792355)).
This paper was edited by Viktor J. Bruckman and reviewed by Jean de Sauvage and one anonymous referee.
Arriba-Rodriguez, L., Villanueva-Balsera, J., Ortega-Fernandez, F., and Rodriguez-Perez, F.: Methods to Evaluate Corrosion in Buried Steel Structures: A Review, Metals, 8, 334, https://doi.org/10.3390/met8050334, 2018.
Ashby, M.: Materials selection in mechanical design, 4th edn., Elsevier, 646 pp., https://doi.org/10.1016/C2009-0-25539-5, 2010.
ASTM International: ASTM G162-18 Standard Practice for Conducting and Evaluating Laboratory Corrosion Tests in Soils, ASTM Committee, ISBN 978-1-6822-1804-0, 2021.
Baboian, R., Munger, C. G., and Treseder, R. S.: Nace Corrosion Engineer's Reference Book, NACE, Houston, TX, ISBN 1-57590-139-0, 1991.
Boban, L., Miše, D., Herceg, S., and Soldo, V.: Application and Design Aspects of Ground Heat Exchangers, Energies, 14, 2134, https://doi.org/10.3390/en14082134, 2021.
Cadelano, G., Bortolin, A., Ferrarini, G., Molinas, B., Giantin, D., Zonta, P., and Bison, P.: Corrosion Detection in Pipelines Using Infrared Thermography: Experiments and Data Processing Methods, J. Nondestruct. Eval., 35, 49, https://doi.org/10.1007/s10921-016-0365-5, 2016.
Cadelano, G., Bortolin, A., Ferrarini, G., Bison, P., Dalla Santa, G., Di Sipio, E., Bernardi, A., and Galgaro, A.: Evaluation of the effect of anti-corrosion coatings on the thermal resistance of ground heat exchangers for shallow geothermal applications, Energies, 14, 2586, https://doi.org/10.3390/en14092586, 2021.
European Commission (EC): Horizon 2020: Cheap GSHPs project, grant no. 657982, EC, https://cordis.europa.eu/project/id/657982/it (last access: 20 June 2022), 2015.
European Commission: Horizon 2020: GEO4CIVHIC project, grant no. 792355, EC, https://cordis.europa.eu/project/id/792355/ (last access: 20 June 2022), 2018.
Ferrarini, G., Bortolin, A., Cadelano, G., Finesso, L., and Bison, P.: Multiple shots averaging in laser flash measurement, Appl. Optics, 59, E72–E79, https://doi.org/10.1364/AO.389564, 2020.
Hähnlein, S., Bayer, P., Ferguson, G., and Blum, P.: Sustainability and policy for the thermal use of shallow geothermal energy, Energ. Policy, 59, 914–925, https://doi.org/10.1016/j.enpol.2013.04.040, 2013.
Mendrinos, D., Katsantonis, S., and Karytsas, C.: Pipe Materials for Borehole Heat Exchangers, in: Proceedings of the European Geothermal Congress 2016, Strasbourg, France, 19–23 September 2016, Contribution no. T-HP-116, 2016.
New York State Department of Transportation, Geotechnical Engineering Bureau: Geotechnical test method gtm-24: Geotechnical test method: test method for determination of ph value of water or soil by pH meter, New York State Department of Transportation, Geotechnical Engineering Bureau, 2015.
Pockele', L., Mezzasalma, G., Righini, D., Vercruysse, J., Cicolin, F., Cadelano, G., Galgaro, A., Dalla Santa, G., De Carli, M., Emmi, G., Mendrinos, D., Pasquali, R., and Bernardi, A.: Innovative Coaxial Heat Exchangers for Shallow Geothermal, in: Proceedings World Geothermal Congress 2020, Reykjavik, Iceland, 24–27 October 2021, Contribution no. 29052, 2020.